Pharmaceutical Water Treatment
Water is one of the major commodities used by the pharmaceutical industry. It is widely used as a raw material, ingredient and solvent in the processing, formulation and manufacture of pharmaceutical products, active pharmaceutical ingredients (API’s) and intermediates, and analytical reagents. It may be present as an excipient or used for reconstruction of products, during synthesis, during production of finished product, or as a cleaning agent for rinsing vessels, equipment, and primary packaging materials etc.
The most stringent requirements apply to water treatment in the pharmaceutical industry. Water must be microbiologically safe, non-pyrogenic, free of organic carbon, and have very low (less than 1 µS/cm) electrical conductivity.
There are many different grades of water used for pharmaceutical purposes. Several are described in USP monographs that specify uses acceptable methods of preparation and quality attributes. These waters can be divided into two general types; bulk waters, which are typically produced on site where they are used, and packaged waters, which are produced, packaged, and sterilised to preserve microbial quality throughout their packaged shelf life. Different grades of water quality are required depending on the different pharmaceutical uses.

Types of water in the pharmaceutical industry
Non-Potable
Water that is not drinking quality but may still be used for many other purposes.
Non potable water is generally all raw water that is untreated such as that from lakes, rivers, ground water springs and ground wells.
Purposes:
- Cleaning outside of the factory
- Used in garden
- Washing vehicles etc.
Potable
Potable water is not suitable for general pharmaceutical use because of the considerable amount of dissolved solids present. These consist mainly of chlorides, sulphates and bicarbonates.
Purposes:
- Drinking water
- Washing and extraction of crude drugs
- Preparation of products for external use
Purified water
Purified water is used in the preparation of all medication containing water expect ampoules, injections and some external preparations such as liniments. Purified water must meet the requirements for ionic and organic chemical purity and must be protected from microbial contamination. The minimum quality of source or feed water for the production of purified water is drinking water.
Purposes:
- Production of non-parenteral preparation/formulation
- Cleaning of certain equipment used in non-parenteral preparation/formulation.
- Cleaning of non-parenteral product contact components
- All types of tests and analysis
- Preparation of some bulk chemicals
- Preparation of media in microbiology laboratories
Preparation techniques:
- Deionization
- Ion Exchange
- Distillation
- Reverse Osmosis
- Filtration, etc.
Water for injection (WFI)
Water for injection is a solvent used in the production of parenteral and other preparations where product endotoxin contact must be controlled, and in other pharmaceutical application. Water for injection is sterile non pyrogenic, distilled water for the preparation of products for parenteral use. It contains no added substance and meets all the requirements for the tests for purified water. It must meet the requirements of the pyrogen test. The finished water must meet all the chemical requirements for purified water as well as an additional bacterial endotoxin specification.
Purposes:
- Production of parenteral preparation/formulation
- Cleaning of parenteral product contact components
Preparation techniques:
- Distillation
- Reverse Osmosis
- Membrane process
Sterile water for injection
Specification as provided in USP monograph for WFI, sterilised and packaged in suitable single dose containers, preferably type 1 glass, not larger than 1000ml.
Purposes:
- Extemporaneous preparation compounding
- Sterile diluent for parenteral products
Preparation techniques:
- Distillation by water for injection (WFI)
Bacteriostatic WFI
Sterile water for injection containing bacteriostatic (antimicrobial) agents. May be packed in single dose containers no larger than 5 ml and in multiple dose containers no larger than 30 ml.
Preparation techniques:
- Sterile water for injection (WFI)
Sterile water for inhalation
WFI that has been packaged and rendered sterile and is intended for use in inhalators and in the preparation of inhalation solutions.
Purposes:
- Preparation of use in inhalators
- Preparation of inhalation solutions
Preparation techniques:
- Sterilisation of water for injection (WFI)
Sterile water for irrigation
Package and sterilised in single dose containers of larger than 1 litre, which allows rapid delivery of its contents.
Purposes:
- Bath and moisten body tissue.
- Performing urologic procedure for surgeon
Preparation techniques:
- Water for injection (WFI)
Water for haemodialysis
Used for haemodialysis applications. It may be packaged and stored in unreactive containers that preclude bacterial entry. “Unreactive containers” implies that the container, especially its water contact surfaces, are not changed in any way by the water, such as by leaching of container related compounds into the water, or by any chemical reaction or corrosion caused by the water. The water contains no added antimicrobials and is not intended for injection.
Purposes:
- Dilution of haemodialysis concentrate solutions
Preparation techniques:
- From safe drinking water
Pure Steam
Sometimes referred to “clean steam”.
Purposes:
- To remove any co-deposited impurity residues
- Air humidification in controlled manufacturing environments
- Steam sterilisation of equipment and porous loads
- Clean in place (CIP) where condensate directly comes into contact with official articles, product contact containers, and surfaces.
Preparation techniques:
- Distillation
- Reverse Osmosis
- Membrane process
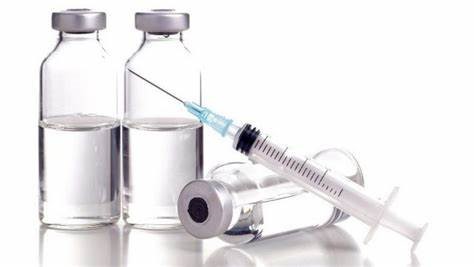
FAQs
What water treatment is required for water for injection systems (WFI)?
Lubron have the experience to supply complete pure water pre-treatment plant to feed WFI, this incorporates Carbon filtration to remove the chlorine, then a water softener to take out the calcium and magnesium, then a reverse osmosis unit, which reduces the conductivity up to 99% and then through Electro de-ionisation (EDI) to achieve water up to 18.0 mOhm’s.
If you would like to find out more about our pharmaceutical water treatment services, get in contact today.
OUR WATER TREATMENT SOLUTIONS FOR DIFFERENT INDUSTRIES
As a partner of many installers, suppliers and consultants, Lubron provides customised water treatment systems for various industries, including food and beverage, textile, chemical, pharmaceutical, electronics, glazing and industrial. Lubron considers the quality requirements for the final product and its specific application, tailoring our advice and consultancy to create a unique solution.
Design and assembly
When designing a process water system, Lubron takes into account all aspects of end use such as: quality requirements, applicable laws and regulations, energy efficiency, maintenance and operating costs. Every installation is professionally designed and manufactured to Lubron’s leading European standards.
Commissioning and maintenance
As a whole project partner, following installation, Lubron takes care of the complete commissioning process, including training on operation and maintenance. Our industry-leading maintenance service supports operations and enhances the life of your investment. Should you experience any problems, you have the assurance of support day or night from our 24/7 response team.